Контроль состояния трубопроводов играет ключевую роль в обеспечении надежной и безопасной работы инженерных систем. Тщательное обследование труб позволяет обнаружить повреждения, уменьшить риск аварий и увеличить срок эксплуатации оборудования. В этой статье мы обсудим основные способы и технологии диагностики трубопроводов, а также дадим рекомендации по их корректному выполнению.
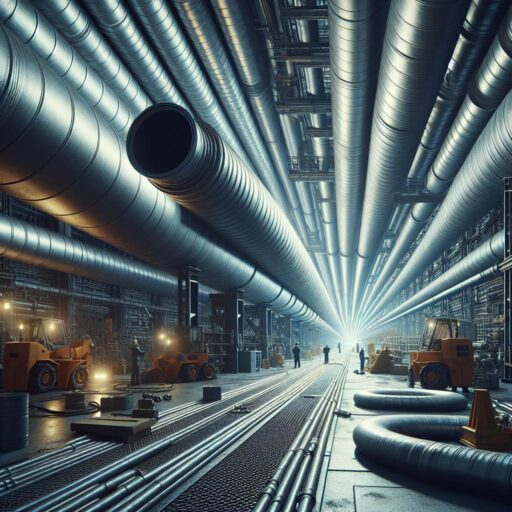
Способы диагностики трубопровода
Существует несколько главных способов проверки трубопроводов, каждый из которых предназначен для конкретных условий эксплуатации и видов дефектов. От правильного подбора метода контроля зависит безопасность и надежность всей системы. Основными методами являются визуальный осмотр, ультразвуковой неразрушающий контроль, рентгеновская томография и гидравлические испытания.
Визуальный осмотр по-прежнему является основным и самым простым методом выявления механических повреждений и признаков коррозии на поверхности труб. Часто его используют вместе с другими техниками для подтверждения первичного заключения.
Ультразвуковое исследование дает возможность обнаружить внутренние повреждения, включая трещины, расслоение металла и коррозионные накопления, которые не видны при обычном внешнем осмотре. Данный способ основан на анализе времени прохождения ультразвуковых волн через материал для определения его состояния.
Гидравлические тесты используются для оценки герметичности и прочности трубопроводных систем. Суть метода состоит в том, что система наполняется водой под повышенным давлением, после чего фиксируется изменение давления за определённый промежуток времени, что позволяет выявить дефекты или протечки.
Метод | Цель | Преимущества | Недостатки |
---|---|---|---|
Визуальный осмотр | Определение поверхностных дефектов | Простой, быстрый и недорогой | Не позволяет выявить внутренние повреждения |
Ультразвуковой контроль | Обнаружение внутренних дефектов | Высокая точность, возможность проверки на просвет | Требует специализированного оборудования и квалифицированного персонала |
Гидравлические испытания | Тестирование на герметичность и прочность | Эффективно выявляет утечки и слабые места | Не выявляет мелкие внутренние дефекты, высокое давление может повредить трубу |
Рентгеновская томография | Всесторонняя оценка состояния материала | Высокая детализация, без повреждений | Высокая стоимость, ограниченная доступность |
Конкретный способ выбирается с учётом характеристик трубопровода, условий его использования и требований нормативных актов. Зачастую для достижения наилучших результатов применяют сочетание нескольких методов контроля.
Особенности визуального осмотра
Визуальный осмотр трубопровода считается одним из наиболее доступных и вместе с тем значимых методов контроля состояния оборудования. Он включает тщательное изучение поверхности труб на наличие видимых повреждений: трещин, участков коррозии, деформаций и признаков протечек. Хотя этот способ достаточно простой, качественное проведение визуального осмотра требует сосредоточенности и профессиональных навыков, поскольку многое зависит от верной оценки и понимания выявленных дефектов.
Особое значение придается стыковым узлам, опорным частям и местам, где трубы находятся под воздействием внешних факторов или агрессивных веществ. Для улучшения качества осмотра используются дополнительные инструменты – такие как эндоскопы и увеличительные устройства, которые дают возможность заглянуть в труднодоступные области и обнаружить незначительные повреждения.
Следует подчеркнуть, что визуальный осмотр обычно является первоначальным этапом диагностики, на базе которого определяется необходимость проведения дальнейших исследований с применением неразрушающих методов. Более того, регулярное выполнение визуального контроля способствует обнаружению ранних признаков износа и предотвращает возникновение серьёзных повреждений.
Для упорядочивания результатов осмотра советуют применять специализированные формы или электронные базы, в которые вносятся данные о выявленных дефектах, их расположении и размерах, а также о проведённых действиях по исправлению недостатков. Этот подход облегчает дальнейший контроль за состоянием трубопровода и подготовку к ремонтным работам.
Применение ультразвукового обследования
Ультразвуковое обследование представляет собой один из наиболее надежных методов неразрушающего контроля трубопроводов. Этот способ основан на применении высокочастотных звуковых волн, которые проходят через материал трубы и отражаются от внутренних дефектов или границ раздела. Благодаря этому оператор получает точные данные о состоянии металла, что позволяет обнаружить такие повреждения, как трещины, пористость, расслоения и участки коррозии, даже если они находятся под слоем защитного покрытия.
Одним из главных достоинств ультразвукового контроля является способность точно измерять толщину стенок трубопровода. Это играет важную роль при оценке уровня износа, который может возникать из-за эрозионных процессов или воздействия химических веществ, переносимых по трубам. Раннее выявление уменьшения толщины стенок помогает организовать ремонтные работы до появления аварийных ситуаций.
Для проведения ультразвукового контроля применяется специализированное оборудование, включающее генератор сигналов, преобразователь и анализатор. Преобразователь передает ультразвуковую волну в трубу, а затем полученные сигналы обрабатываются для визуализации и интерпретации результатов. Современные портативные приборы обладают цифровыми дисплеями и программным обеспечением, что позволяет быстро и точно выполнять обследование даже на выезде.
Внизу приведена таблица с ключевыми параметрами ультразвуковой диагностики, оказывающими влияние на качество инспекции:
Параметр | Описание | Влияние на результат |
---|---|---|
Частотный диапазон ультразвука | Определяет длину волны и глубину проникновения в материал | Высокая частота обеспечивает лучшее разрешение, низкая — большую глубину проникновения |
Тип преобразующего устройства | Форма и размеры ультразвукового излучателя | Влияет на чувствительность и область сканирования |
Режим эксплуатации | Отражательный, пропускной или фазовый методы | Определяет вид и глубину обнаруживаемых дефектов |
Для увеличения точности диагностики выполняется калибровка приборов на эталонных образцах и использование специальных гелей, улучшающих контакт между преобразователем и трубной поверхностью. Помимо этого, ультразвуковое обследование может совмещаться с другими неразрушающими методами, например, магнитопорошковым или вихретоковым контролем, что позволяет всесторонне оценить техническое состояние трубопровода.
Проведение гидравлических тестов трубопровода
Гидравлические тесты трубопровода считаются одним из самых надёжных методов проверки прочности и герметичности системы. В ходе испытаний трубопровод заполняют водой или другой рабочей жидкостью, затем на него воздействуют давлением, превышающим рабочее с учётом установленного нормативами коэффициента. Это позволяет максимально смоделировать условия возможной аварии и обнаружить уязвимые участки конструкции до начала эксплуатации.
Главное достоинство гидравлических испытаний заключается в возможности обнаружения скрытых повреждений, таких как мелкие трещины, протечки и дефекты в сварных швах. Особое внимание уделяется контрольным зонам – фланцевым соединениям, изгибам и участкам с изменяющимся диаметром, так как именно там чаще всего возникают неполадки. Испытания должны проводиться по строго установленной технологии и с соблюдением требований безопасности, чтобы не повредить трубопровод и гарантировать достоверность результатов.
Для успешного проведения гидравлических испытаний необходимо тщательно подготовить трубопровод: избавиться от воздушных пробок, проверить отсутствие загрязнений и обеспечить крепкое закрепление всех соединений. Давление подаётся плавно, с контролируемым увеличением, и удерживается в течение времени, установленного нормативами. Если в процессе испытания наблюдается снижение давления или выявляются протечки, это говорит о наличии дефектов, требующих детального обследования и ремонта.
Пример последовательности проведения гидравлических испытаний представлен ниже:
- Подготовка и очистка трубопровода
- Монтаж манометров и контрольно-измерительного оборудования
- Удаление воздуха и заполнение водой
- Плавное повышение давления до необходимого уровня
- Поддержание давления с контролем параметров
- Снижение давления и проведение анализа полученных данных
- Оформление протоколов испытаний
Широкое использование гидравлических испытаний в промышленности, строительстве и эксплуатации инженерных систем свидетельствует об их эффективности. Однако необходимо помнить, что такие испытания способны вызвать микротрещины в уязвимых зонах, поэтому следует выполнять их с учётом характеристик материала и особенностей трубопровода.
Оборудование и инструменты для диагностики трубопровода
Для надежного обследования трубопровода требуется применение специального инструмента и оборудования, обеспечивающего точность диагностики и безопасность выполнения работ. Современная промышленность предоставляет разнообразные приборы, приспособленные под разные методы контроля, что существенно упрощает обнаружение дефектов на начальных этапах и снижает вероятность аварийных происшествий.
Ключевые виды оборудования, применяемого для диагностики трубопроводов, включают в себя:
- Визуальные приборы — эндоскопы, видеокамеры и оптические лупы, которые позволяют обследовать труднодоступные места без демонтажа системы.
- Ультразвуковые дефектоскопы — аппараты с разными типами преобразователей для определения толщины стенок и выявления внутренних дефектов.
- Оборудование для гидравлических тестов — манометры высокого давления, насосы и клапаны, обеспечивающие надежное и точное создание требуемого рабочего давления в системе.
- Магнитопорошковое и вихретоковое оборудование — приборы, предназначенные для обнаружения поверхностных и скрытых трещин, основанные на свойствах материала и электромагнитных принципах.
Следует подчеркнуть, что современные автоматизированные диагностические системы оснащены программным обеспечением для обработки и анализа данных, что существенно уменьшает риск ошибок со стороны человека и ускоряет проверку.
Помимо технических устройств, важную роль в эффективной проверке играют опытные операторы, обладающие умениями обращения с техникой и знаниями по анализу дефектов. Постоянное обучение и подтверждение квалификации специалистов гарантируют надежность диагностики и безопасность процесса.
Приборы и сенсоры для выявления повреждений
Для качественного выявления дефектов в трубопроводах применяются разнообразные датчики и устройства, обладающие своими техническими особенностями и сферами использования. Подбор конкретного оборудования определяется видом дефектов, которые требуется обнаружить, условиями эксплуатации, а также финансовыми рамками и необходимой точностью диагностирования. Современные технологии предоставляют широкий выбор приборов, обеспечивающих как поверхностный, так и глубокий контроль состояния труб.
Магнитные и электромагнитные датчики являются одними из наиболее часто применяемых устройств для обнаружения трещин, расслоений и коррозийных дефектов на металлах. Их работа базируется на изменениях магнитного поля или электрических свойств материала при повреждении целостности. Эти датчики характеризуются высокой чувствительностью и позволяют проводить обследование без прямого контакта с поверхностью.
Вихретоковые устройства являются надежным средством для диагностики электропроводящих материалов. Они создают высокочастотное магнитное поле, которое индуцирует вихревые токи внутри металла. Изменения в их плотности указывают на присутствие внутренних или поверхностных дефектов. Благодаря своей высокой скорости сканирования, вихретоковый контроль широко используется для проверки сварных швов, труб и различных конструктивных элементов.
Для проверки трубопроводов больших диаметров и при сложных условиях обычно применяют комбинированные системы, объединяющие несколько методов, что даёт возможность более полно оценить состояние материалов. Одним из таких вариантов являются инструментальные комплексы с встроенными ультразвуковыми и магнитопорошковыми блоками, которые позволяют выявлять разнообразные дефекты одновременно.
Внизу приведена таблица с ориентировочным описанием главных типов датчиков и устройств для выявления дефектов:
Вид датчика | Принцип действия | Сфера использования | Преимущества |
---|---|---|---|
Магнитные датчики | Изменение магнитного поля при повреждении структуры | Металлические трубопроводы, обнаружение трещин и коррозии | Высокая чувствительность, контактный и бесконтактный режимы работы |
Вихретоковые приборы | Создание и анализ вихревых токов в металле | Сварные швы, стенки труб, листовой металл | Быстрая диагностика, выявление мельчайших дефектов |
Ультразвуковые датчики | Определение времени прохождения ультразвуковых волн | Толщина стенок, внутренние повреждения | Точное сканирование скрытых областей без разрушения |
Магнитопорошковый метод | Накопление магнитного порошка в зонах дефектов | Обнаружение поверхностных и подповерхностных трещин | Простота, надёжность и визуальное выявление |
Постоянный прогресс технологий в сфере контроля трубопроводов приводит к появлению новых типов датчиков с усовершенствованными параметрами, что способствует увеличению безопасности и эффективности использования инженерных систем. Внедрение этих устройств в автоматизированные системы сбора и обработки информации значительно облегчает наблюдение за состоянием объектов и своевременное принятие решений по их обслуживанию.
Системы автоматической диагностики
Современные автоматизированные системы диагностики трубопроводов представляют собой комплексные аппаратно-программные комплексы, значительно облегчающие процесс контроля и оценки состояния инженерных сетей. Они включают в себя разнообразные методы проверки — от ультразвукового и магнитопорошкового до вихретокового и визуального — собранные в единую платформу, что позволяет интегрировать и синхронизировать данные для всестороннего анализа.
Главным достоинством подобных систем выступает сокращение влияния человеческого фактора, что уменьшает вероятность ошибок, улучшает точность диагностики и ускоряет обработку информации. Благодаря автоматическому сбору данных с датчиков, их анализу и интерпретации специалисты получают подробные отчёты, графики износа и рекомендации для планирования ремонтных мероприятий, что способствует более рациональному управлению ресурсами и предотвращению аварий.
Обычно в автоматизированные системы диагностики входят такие компоненты:
- различные типы датчиков для сбора информации о физическом состоянии трубопровода;
- беспроводные устройства передачи данных для отправки информации в облачные сервисы или локальные серверы;
- программные системы с алгоритмами анализа, моделирования и прогнозирования состояния;
- операторский интерфейс с удобными панелями для мониторинга и визуализации;
- средства автоматизированного оповещения при обнаружении отклонений и возможных угроз.
Использование подобных технологий особенно важно для трубопроводов значительной длины и сложной конструкции, когда привычные способы контроля оказываются трудоёмкими и затратными. Постоянный сбор и обработка данных в режиме реального времени позволяют компаниям гарантировать своевременное техническое обслуживание и повысить общую безопасность эксплуатации объектов.
Как осуществляется проверка трубопровода
Корректная последовательность проверки трубопровода начинается с тщательной подготовки объекта и сопутствующей документации. Прежде всего следует изучить техническую документацию, включающую схемы трубопровода, сведения о материалах и проведённых ранее ремонтах. Это даёт возможность выявить важные участки для контроля и подобрать наиболее подходящие методы диагностики.
Далее проводится непосредственная подготовка трубопровода к проведению проверки: отключение системы от источников давления, очистка внутренних и внешних поверхностей от загрязнений, а также обеспечение свободного доступа к ключевым контрольным точкам. Необходимо убедиться, что все компоненты системы надежно закреплены и исключается вероятность случайного включения или запуска процессов во время осмотра.
Далее переходят к ключевым этапам диагностики, которые предполагают поочередное использование выбранных способов контроля. Чаще всего проверка стартует с визуального осмотра, позволяющего оперативно обнаружить явные дефекты. Затем выполняют неразрушающие методы испытаний, например, ультразвуковой или вихретоковый контроль, чтобы подробно оценить состояние трубы и сварных соединений.
На завершающем этапе выполняют гидравлические испытания с документированием полученных данных. Для каждого теста составляется детальный протокол, в котором указываются давление, продолжительность выдержки, выявленные отклонения и рекомендации по ремонту или усовершенствованиям. Такой методичный и структурированный подход гарантирует высокую точность диагностики и помогает вовремя принять меры для продления эксплуатационного срока трубопровода.
Этап подготовки
Этап подготовки к проверке трубопровода является важнейшим для гарантии точности и безопасного проведения всех дальнейших исследований. Он стартует с детального изучения технической документации, где указаны характеристики системы трубопроводов: материалы, толщина стенок, виды сварных соединений и эксплуатационные условия. Такой анализ способствует выбору наиболее подходящих методов и технологий диагностики, а также позволяет выявить зоны, нуждающиеся в повышенном внимании.
Ключевым этапом на данном шаге становится анализ текущего состояния трубопровода, опираясь на результаты прежних инспекций и эксплуатационные данные. Такой подход помогает обнаружить возможные проблемные участки и уменьшить время, затрачиваемое на выявление дефектов в ходе основной проверки. Помимо этого, на этапе подготовки учитываются меры безопасности, направленные на снижение рисков для сотрудников и техники во время проведения диагностики.
Перед началом выполнения работ проводится проверка доступа к трубопроводу и обустройство рабочих зон. Особое значение придается обеспечению энергоснабжения и отключению гидравлических систем, чтобы предотвратить случайное включение оборудования во время осмотра. На этом этапе также устанавливаются временные ограждения, защитные таблички и другие средства безопасности труда.
Чтобы улучшить процесс проверки, рекомендуется разработать детальный технологический план, где будет отражена очередность действий, назначены ответственные и указаны требуемые ресурсы. Обычно такую документацию оформляют в табличной форме:
Подготовительный этап | Выполняемые действия | Ответственные лица | Сроки проведения |
---|---|---|---|
Изучение технической документации | Анализ паспортов и чертежей трубопровода | Инженер-технолог | 1-2 дня |
Оценка текущего состояния | Сбор информации о предыдущих проверках и ремонтах | Сервисный инженер | 1 день |
Обеспечение доступа и мер безопасности | Отключение систем и установка ограждений | Технический персонал | 1 день |
Разработка плана проверки | Определение последовательности работ и распределение обязанностей | Руководитель проекта | 1 день |
Скрупулезная подготовка улучшает качество диагностики и уменьшает риск аварий во время обследования. К тому же, она помогает экономить ресурсы и уменьшает периоды простоя системы, что имеет особое значение для промышленных предприятий с круглосуточным режимом работы.
Методы проведения тестирования и измерительных процессов
Тестирование и измерения при проверке трубопроводов осуществляются с обязательным соблюдением регламентированных процедур, которые обеспечивают получение надежных и объективных сведений о техническом состоянии конструкции. Каждая методика контроля предполагает строгую последовательность этапов, начиная с подготовки приборов и завершая оценкой полученных данных. Значимым является то, чтобы весь процесс контролировался квалифицированными и опытными специалистами.
Перед проведением замеров важно надёжно закрепить датчики и приборы на трубе, а также выполнить калибровку оборудования в соответствии с установленными нормативами. Это обеспечивает корректную интерпретацию сигналов и снижает риск ошибок, вызванных внешними факторами, такими как вибрация или изменения температуры. При выполнении ультразвукового контроля, например, особое внимание уделяется точному соблюдению угла ввода ультразвуковой волны для обеспечения максимальной чувствительности к дефектам.
При проведении замеров часто применяют пошаговое либо непрерывное сканирование обследуемых областей. Данные при этом собираются в соответствии с заранее установленной координатной сеткой, что даёт возможность составить подробную карту состояния трубопровода и избежать пропуска опасных мест. Подчёркивается значимость повторных измерений для подтверждения надёжности полученных результатов и отслеживания динамики изменения параметров.
Особое значение придается параметрам тестирования — например, при проведении гидравлических испытаний давление увеличивается постепенно, а время выдержки контролируется с помощью манометров и таймеров. Если параметры выходят за установленные нормы, испытание останавливают для дополнительного осмотра и выяснения причин неисправности. Независимо от выбранного метода, каждый этап фиксируется в протоколе, что гарантирует прозрачность процесса и возможность дальнейшего анализа.
Современные технологии включают применение цифровых систем сбора информации, которые автоматически отправляют измеренные данные на рабочие места специалистов. Это даёт возможность быстро обнаруживать отклонения и принимать меры по дополнительному контролю или ремонту.
Распространённые повреждения трубопроводов и методы их обнаружения
Трубопроводы, являясь ключевыми компонентами инженерных систем, подвергаются различным повреждениям, которые значительно отражаются на их работоспособности и безопасности использования. Чаще всего встречаются коррозионные и механические дефекты, которые могут вызвать протечки, ослабление конструкции и в итоге привести к аварийным происшествиям.
Коррозия возникает не только снаружи труб, но и может развиваться внутри них, особенно при транспортировке агрессивных веществ. Для выявления подобных повреждений используются ультразвуковые методы контроля, позволяющие обнаруживать зоны со сниженной толщиной стенок. Кроме того, магнитопорошковый и вихретоковый способы помогают выявлять коррозионные трещины и другие мелкие дефекты, которые трудно рассмотреть визуально.
Вибрации, внешние воздействия и ошибки при монтаже могут привести к механическим повреждениям, таким как вмятины, трещины и царапины. Для выявления этих дефектов часто применяют визуальный осмотр с использованием эндоскопов и видеокамер, а также магнитные датчики, способные обнаруживать деформации металлической структуры. Особое внимание при проверке уделяется сварным швам и фитингам, поскольку именно в этих участках нагрузка максимально сосредоточена.
Вид дефекта | Характеристика | Способы обнаружения |
---|---|---|
Коррозия | Повреждения, вызванные химическим воздействием и процессами окисления | Ультразвуковая диагностика, метод магнитного порошка, визуальный осмотр |
Трещины | Мелкие и крупные разрывы в металле, уменьшающие его прочностные свойства | Метод магнитного порошка, вихретоковый контроль, ультразвуковое обследование |
Механические деформации | Вмятины, изгибы и иные изменения формы под действием внешних сил | Визуальный контроль, использование магнитных сенсоров, эндоскопия |
Утечки | Потеря транспортируемой среды вследствие повреждений и дефектов | Гидравлические тесты, приборы для акустической эмиссии |
К методам выявления утечек особого характера относятся гидравлические тесты с мониторингом снижения давления, а также использование технологий акустической эмиссии, улавливающих звуковые сигналы, возникающие при нарушении герметичности. Этот способ особенно хорошо подходит для обнаружения микроскопических подтеков, которые иными методами трудно обнаружить.
Комплексная диагностика, включающая несколько методов, даёт возможность вовремя выявлять скрытые повреждения, что существенно снижает риск аварий и уменьшает расходы на ремонт. Постоянное отслеживание состояния трубопровода с использованием современных технологий обеспечивает надежную и безопасную работу.
Механические повреждения и коррозия
Главными факторами раннего износа трубопроводов являются коррозия и механические повреждения, особенно заметные в агрессивных условиях и при интенсивной эксплуатации. Коррозия может происходить как снаружи, так и внутри трубы, часто развиваясь незаметно, что приводит к постепенному уменьшению толщины стенок и снижению прочности материала.
Для оценки состояния труб на наличие коррозионных повреждений используют ультразвуковые методы толщинометрии, которые дают возможность точно определить толщину металла в разных местах. Такой способ позволяет выявить зоны, нуждающиеся в ремонте или замене. Немаловажное значение имеет контроль химического состава и условий эксплуатации, поскольку грамотный подбор материала и антикоррозионных покрытий значительно уменьшает вероятность возникновения коррозии.
В основном механические повреждения появляются из-за воздействия внешних факторов: ударов, вибраций, температурных расширений и ошибок при монтаже. Такие дефекты могут проявляться как вмятины, трещины, деформации или потертости, которые влияют на целостность трубы и увеличивают риск утечек. Для быстрой и точной диагностики механических повреждений применяются инструментальные методы, например, магнитный контроль и металлографический анализ срезов, позволяющие оценить характер повреждений.
Для предотвращения и контроля последствий механических повреждений обычно применяют комплексные методы, которые охватывают не только диагностику, но и профилактические мероприятия: монтаж амортизирующих опор, мониторинг вибраций, а также правильную установку и перевозку оборудования. Раннее обнаружение и устранение подобных дефектов значительно увеличивает срок эксплуатации трубопровода и помогает избежать аварий.
Проблемы с целостностью и утечки
Повреждения трубопроводов считаются одними из самых серьёзных дефектов, поскольку могут вызвать серьёзные аварии и экологические катастрофы. Причинами таких повреждений становятся различные факторы — от механических воздействий и коррозийных процессов до ошибок при установке и продолжительной работы под высокими нагрузками. Помимо ухудшения рабочих характеристик, подобные нарушения повышают вероятность утечки транспортируемых веществ, что влечёт за собой не только финансовые потери, но и опасность для здоровья людей и окружающей среды.
Утечки могут проявляться в двух формах: явной и скрытой. Явные протечки заметны с помощью визуального осмотра — это капли или струйки жидкости. Тем не менее, наиболее опасны скрытые утечки, которые происходят внутри защитных оболочек или в грунте и могут оставаться незамеченными долгое время без применения специальных методов контроля. Для их обнаружения используются специальные устройства, регистрирующие малейшие изменения давления, звуковые сигналы и химические параметры окружающей среды.
Современные диагностические технологии ориентированы не только на выявление нарушения целостности, но и на точное определение места утечки. Особенно результативным в этом аспекте считается метод акустической эмиссии — сенсоры улавливают звуки, возникающие при пробое или появлении трещины. Полученные данные обрабатываются и анализируются в реальном времени, что даёт возможность быстро принять меры по устранению неполадок.
Не менее значимым способом обнаружения утечек является применение газовых трассеров и химических индикаторов, которые добавляются в транспортируемую среду и фиксируются анализаторами на поверхности трубопровода, даже если утечка происходит под землёй или внутри изоляции. Такой комплексный метод выявления утечек значительно повышает безопасность эксплуатации и минимизирует риски вреда для персонала и окружающей среды.
Стандарты и нормативные требования к проверке трубопроводов
Стандарты и нормативные требования к проверке трубопроводов имеют важное значение для безопасности и надёжного функционирования систем. Они включают обязательные правила и рекомендации, которые регламентируют методы диагностики, периодичность осмотров, критерии оценки состояния труб, а также требования к квалификации специалистов и техническому оборудованию. Следование этим нормам помогает снизить вероятность аварий, уменьшить финансовые затраты и продлить срок эксплуатации трубопроводных систем.
В различных странах и отраслях промышленности существуют собственные нормативные акты, однако большинство из них опираются на признанные мировые стандарты, такие как ISO (Международная организация по стандартизации), ASME (Американское общество инженеров-механиков) и API (Американский институт нефти). Эти документы определяют единые требования к проведению визуальных и инструментальных обследований, испытаний на герметичность, методам неразрушающего контроля, а также к оформлению технической документации.
Для гарантии системного подхода к инспекциям трубопровода нормативные акты устанавливают следующие ключевые моменты:
- частоту и типы диагностики, зависящие от категории и назначения трубопровода;
- требования к техническому состоянию оборудования и измерительных средств;
- квалификацию и аттестацию специалистов, выполняющих обследования;
- регламентацию процедур по обнаружению и классификации дефектов;
- правила оформления актов о техническом состоянии и проведении ремонтных работ;
- требования по обеспечению безопасности на рабочих местах во время проверки.
В таблице ниже представлен пример того, как можно распределить частоту проверок различных видов трубопроводов согласно стандартам отрасли:
Вид трубопровода | Первичная инспекция | Интервал последующих проверок | Основные методы обследования |
---|---|---|---|
Промышленные трубопроводы нефтегазовой отрасли | Перед началом эксплуатации | 1 раз в 1-2 года | Визуальный осмотр, ультразвуковое тестирование, гидравлические испытания |
Коммунальные сети водоснабжения | После установки | 1 раз в 3-5 лет | Визуальный осмотр, гидроиспытания |
Трубопроводы химической отрасли | До запуска в работу | 1 раз в 6-12 месяцев | Вихретоковый контроль, магнитно-порошковый анализ, ультразвуковое сканирование |
Важным элементом нормативных требований является поддержание подробной технической документации, отражающей каждый этап проверки, измерительные данные и принятые корректирующие меры. Такой метод обеспечивает возможность отслеживания технического состояния трубопровода на всех этапах его эксплуатации и помогает принимать обоснованные решения по ремонту и обновлению. Кроме того, стандарты требуют обязательного уведомления государственных и контролирующих органов о результатах инспекций при выявлении серьезных дефектов.
Соблюдение нормативных требований является не просто юридическим обязательством, но и гарантией безопасности сотрудников, защиты окружающей среды и минимизации финансовых рисков. В связи с этим компании, работающие с трубопроводами, обязаны постоянно обновлять свои знания о действующих стандартах и применять передовые методы контроля и диагностики, учитывая современные технологические решения.
Роль постоянного осмотра трубопроводов в обеспечении безопасности и надежной работы
Периодический осмотр трубопровода значительно улучшает безопасность эксплуатации объектов. Раннее обнаружение даже незначительных повреждений помогает избежать аварий и утечек, которые могут угрожать жизни сотрудников и окружающей среде. Кроме того, регулярное наблюдение за состоянием труб снижает вероятность внезапных поломок и разрушений, поддерживая целостность системы.
Регулярные осмотры гарантируют сохранение технических параметров трубопроводов в пределах установленных норм, что оказывает непосредственное влияние на надежность и эффективность функционирования всей инженерной системы. Благодаря этому уменьшается время простоев и сокращаются затраты на внеплановые ремонты, так как обслуживание проводится по заранее составленному графику, а не экстренно и с большими расходами.
Регулярный контроль помогает оптимизировать планы технического обслуживания и модернизации оборудования, опираясь на текущее состояние трубопроводных систем. Это обеспечивает более эффективное распределение ресурсов и улучшает эксплуатационные показатели. Внедрение системы мониторинга состояния с применением современных диагностических технологий снижает нагрузку на сотрудников и повышает качество принимаемых решений.
Следовательно, регулярная проверка трубопроводов обеспечивает не только безопасность и стабильность, но и приносит экономическую пользу, поддерживая долговременную и бесперебойную работу предприятий разных отраслей промышленности.
Актуальные направления и новшества в сфере испытания трубопроводов
В современных направлениях проверки трубопроводов главной задачей становится интеграция цифровых технологий и автоматизации, что значительно улучшает точность диагностики и сокращает время обследований. Широко применяются системы мониторинга в режиме реального времени с использованием датчиков интернета вещей (IoT), которые обеспечивают постоянный сбор информации о рабочих параметрах и состоянии трубопровода. Этот метод помогает вовремя выявлять отклонения и позволяет прогнозировать развитие повреждений с помощью аналитических моделей и технологий искусственного интеллекта.
Одним из важнейших инновационных подходов стало использование роботов и беспилотных аппаратов для обследования удалённых и труднодоступных частей трубопроводных систем. Эти устройства оборудованы камерами с высоким разрешением, а также ультразвуковыми и магнитными сенсорами, что позволяет выполнять комплексную диагностику без остановки работы или разбора оборудования. Данная технология снижает риски для работников и уменьшает расходы на эксплуатацию.
Методы обработки и визуализации данных, такие как трёхмерное моделирование и виртуальная реальность, приобретают всё большее значение. Применение этих технологий помогает специалистам точнее оценивать состояние трубопроводов, выявлять дефекты с высокой точностью и детально планировать ремонт. Помимо этого, современные алгоритмы машинного обучения широко применяются для классификации повреждений и прогнозирования оставшегося ресурса труб.
В соответствии с международным опытом, компании начинают применять стандарты цифровой паспортизации трубопроводов, при которых вся информация о техническом состоянии, проведённых проверках и ремонтах сохраняется в централизованных электронных базах данных. Такая организация данных обеспечивает прозрачность эксплуатации, облегчает контроль для регулирующих органов и способствует повышению эффективности управления активами.
Ленинградская система отопления — это одна из наиболее распространенных и проверенных временем схем отопления частных домов и квартир. Данная система…
Полная замена стояков отопления в доме является важным мероприятием, которое может существенно повысить комфорт и безопасность проживания. Вот несколько причин,…
Газовое отопление является одним из наиболее популярных способов отопления жилых помещений. Однако, несмотря на надежность и долговечность современных систем, со…
Ремонт труб автономного отопления представляет собой важный этап в поддержании стабильной работы системы и предотвращении аварийных ситуаций. В условиях автономного…
Замена трубы водопровода в частном доме: все, что нужно знать. Когда речь заходит о комфорте в нашем доме, водопровод играет…
Ремонт и замена отопления в Истре: современные технологии и комфорт в вашем доме Современные технологии продолжают проникать во все сферы…
Течь в металлической трубе отопления может стать причиной значительных теплопотерь и даже аварийных ситуаций. В этом руководстве мы рассмотрим основные…
Течь трубы отопления под давлением – это серьезная проблема, требующая оперативного вмешательства. В случае обнаружения утечки, важно действовать быстро и…
Пластиковые трубы широко применяются в системах отопления и водоснабжения благодаря своей долговечности, устойчивости к коррозии и простоте монтажа. Однако даже…
Течь в трубе отопления — это неприятность, которая может возникнуть внезапно и нарушить привычный ритм жизни. Однако не стоит паниковать,…
Проблема течи в стыке трубы отопления может стать серьезной проблемой, если не принять своевременные меры. В этом руководстве мы рассмотрим…
Если в трубе отопления течет вода, это может привести к серьезным проблемам, таким как затопление помещения и повреждение оборудования. Чтобы…
Пластиковые трубы отопления становятся все более популярными благодаря своим долговечности, надежности и простоте в установке. Однако, несмотря на их преимущества,…
Течь трубы отопления – это проблема, которая может возникнуть в любой момент, особенно если система отопления установлена давно. В таких…
Текущая труба отопления может стать серьезной проблемой для любого дома. Она не только снижает эффективность отопления, но и представляет опасность…
Заделка течи в трубе отопления требует оперативного и правильного подхода. В случае возникновения утечки необходимо прекратить подачу тепла, чтобы избежать…
Течь в трубе отопления может стать серьезной проблемой, особенно если она происходит в зимний период. Для устранения этой неполадки необходимо…
Если в вашей системе отопления обнаружилась течь, это может привести к значительным финансовым затратам и дискомфорту в доме. Прежде всего,…
В многоквартирных домах и частных коттеджах замена старых труб отопления является важным и необходимым мероприятием для поддержания комфортной температуры и…
Газовый котел является важным элементом отопительной системы, обеспечивающим тепло и уют в доме. Однако, как и любое другое оборудование, он…
Ремонт газового котла в Головино: важные аспекты и меры безопасности Ремонт газового котла в Головино — это важный и ответственный…
Газовый котел является неотъемлемой частью системы отопления в частных домах, и его неисправность может привести к серьезным последствиям. В деревне…
Ремонт газового котла Высоково: основные этапы и особенности Газовые котлы являются неотъемлемой частью отопительных систем, обеспечивая комфортное проживание в частных…
Газовые котлы являются неотъемлемой частью отопительных систем в большинстве современных домов. Они обеспечивают комфортную температуру и уют, и их правильное…
Итог
Проверка трубопровода представляет собой важную процедуру, гарантирующую безопасность и надежность работы инженерных систем. Регулярное проведение диагностики помогает вовремя обнаруживать повреждения, что дает возможность быстро принимать меры для их устранения и предотвращения серьезных аварий. Эффективный контроль базируется на комплексном подходе, включающем визуальный осмотр, неразрушающие методы проверки и функциональные тесты.
Развитие диагностических технологий и применение автоматизированных систем значительно увеличивают эффективность контроля и уменьшают время, необходимое для проведения инспекций. Внедрение цифровых средств в процедуры мониторинга помогает получить всестороннюю информацию о техническом состоянии трубопроводов и позволяет прогнозировать возможные угрозы.
Особенно важно строго придерживаться норм и стандартов, регулирующих инспекцию трубопроводов, поскольку их выполнение гарантирует согласованность действий и выполнение требований безопасности. Также внимание следует уделять профессионализму и регулярному развитию квалификации специалистов, проводящих обследования, что имеет решающее значение для качественной диагностики.
В итоге, надежная система проверки трубопроводов обеспечивает не только стабильную работу и увеличивает срок эксплуатации оборудования, но и позволяет сократить расходы на ремонт и устранение последствий аварий. Это делает процедуру проверки ключевым аспектом эксплуатационной стратегии любой компании, нацеленной на безопасное и экономически эффективное функционирование своих объектов.
Ремонт труб отопления в коттедже является важной задачей, особенно в условиях суровой зимы, когда системы отопления должны работать бесперебойно. В…